NP3® (Electroless Nickel / PTFE)
Process Specifications
- AMS 2454
- GPS 3117-1
- M7019883
- HP4-90
- EMS 52545
- P.S. 10-27
- 70B995447
All NP3® coatings are RoHS compliant.
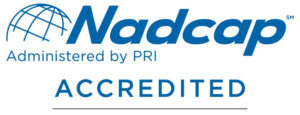
Aerospace Quality Systems
Chemical Processing
About NP3®
NP3® is a surface treatment for various metals and alloys that combines sub-micron particles of PTFE with Electroless Nickel (EN/PTFE). The result is an accurately applied, dry lubricated, low friction surface that is corrosion resistant, extremely hard and resistant to wear.
The PTFE is evenly distributed throughout and locked into the nickel matrix creating a true and stable composite. As wear occurs fresh particles of PTFE are exposed to keep the surface lubricated. This lubrication is available as long as the integrity of the coating is intact.
One of the major benefits of the NP3® coating is that it resists fouling compounds on firearms, unlike other hard coatings that continuously build up carbon deposits affecting performance. The durability, longevity and reduced maintenance are unmatched by other comparably priced firearms coatings.
Being a true dry film lube coating, NP3® can be used without additional lubricants. This further minimizes unwanted buildup of foreign matter. A minimal amount of light oil can be utilized to lower the coefficient of friction even farther if desired.
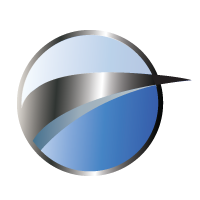
NP3® Technical Data
NP3® EN / PTFE Deposit Performance Facts
Composition | Nickel | 80 – 84% by weight |
Phosphorus | 9 – 11% by weight | |
PTFE | 7 – 9% by weight (19–25% by volume) |
|
Density | 6.5 g/cm3 | |
Hardness | As-Plated | 300-350 HV100 (32-35 RC) |
Heat Treated@300°C for 4 hrs | 400-450 HV100 (42-46 RC) |
|
Melting Temperature | Nickel Phosphorus Alloy | 1650°F, 900°C |
PTFE | 620°F, 325° C | |
Co-Efficient of Friction | LFW-1, ASTM D-2714 | |
Wet (white oil) | .07 – 0.10 | |
Dry | 0.1 – .2 | |
Wear Resistance | Excellent, Mild Load/Sliding Wear Conditions | |
Abrasion Resistance | Taber Abrasive Test | CS – 10 Wheel; 1000g load Weight loss, mg/1000 cycles 20 |
Corrosion Resistance | ASTM B | 117 Salt Spray |
0.3 mil | 96 hours | |
1.0 mil | 500 hours | |
Electrical Resistance | Ohms Per Square | 0.06 ohm (0.84 mil deposit) |
Additional Services
- Masking
- Abrasive blasting, sand or glass
- Pre-plate Stress Relief and Hydrogen Embrittlement Baking
- Expediting
- Aluminum Oxide
- Glass Bead